JC Machining offer an unrivaled range of high precision CNC grinding services to our global clients

CNC Optical Profile Grinding & Cylindrical Grinding Services
We provide a wide range of CNC grinding services to our global customers, including Optical Profile Grinding and Tungsten Carbide Grinding. In this article we will focus on optical profile grinding and cylindrical grinding as two types of CNC grinding of critical importance to manufacturing industries in 2023.
Table of Contents
Optical Profile Grinding
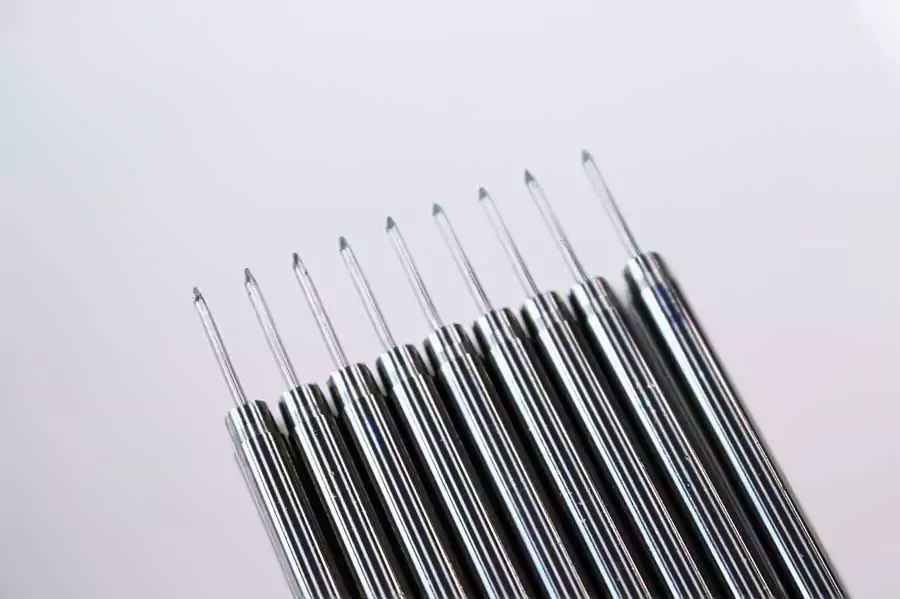
Optical profile grinding technology is used to manufacture complex and intricate molds and cutting tools with very high precision. A historic trend that continues through 2023 and for the foreseeable future is for die parts and tools to become increasingly complex and precise. The demand for CNC grinding of complex shapes with very high surface accuracy is steadily increasing.
Optical profile grinders enable the operator to view the CNC grinding process on a magnified visual display, and use this to check progress against the desired template. We use the WAIDA SPG-X optical profile grinder to manufacture high precision parts because it has state of the art features including extremely clear LED image projection technology.
Optical profile grinding can be used to manufacture long, narrow, toothed, splined or slotted components and is a flexible technique that is used to grind both external and internal teeth when very precise internal or external profiles are required. Typical applications of optical profile grinding include:
- high precision mold parts
- cutting tools
- precision machine components
- punches and dies
This technique is well suited to prototyping and series production of very fine components where precision finishing is of utmost importance. Cutting wheel technology can increase the applications for profile grinding, including thin wall applications using high precision ceramic bonded Polycrystalline Diamond (PCD) and Polycrystalline Cubic Boron Nitride (PCBN / CBN) grinding wheels.
Cylindrical Grinding
External cylindrical grinding is generally used for grinding workpieces that are symmetrical around the axis of rotation, with the workpiece clamped between centers. Types of cylindrical grinding are defined by how the workpiece is clamped and the direction of the feed. Cylindrical grinding is most suitable for:
- objects with a central axis of rotation
- production grinding of a series of identical objects
- precision finishing of cylindrical objects
Cylindrical grinding is a versatile technique that can be used for internal and external grinding, form grinding, and centerless grinding. External cylindrical grinding is commonly used to manufacture the following standard components:
- jet needles for injection systems
- bearing seats of camshafts
- valve tappets for the automotive industry
Because the standard clamping system for external cylindrical grinding is between centers, the workpiece must be precisely centered. Long, thin, or heavy workpieces must be adequately supported to ensure accurate geometry without distortion or vibration. Variations on cylindrical grinding include:
- plunge grinding
- creep feed grinding
- oscillation grinding
- centerless through feed grinding
- centerless plunge grinding
Cylindrical grinding is used for series production of precision tools including drills and cutters. In this application, peel grinding is commonly used to improve production speed and accuracy. Peel grinding has higher infeed characteristics with fewer cuts resulting in an oscillating cutting movement. Our Rollomatic Shapesmart NP5 pinch/peel grinding machines are ideal for this application.
High Precision CNC Grinding Technology
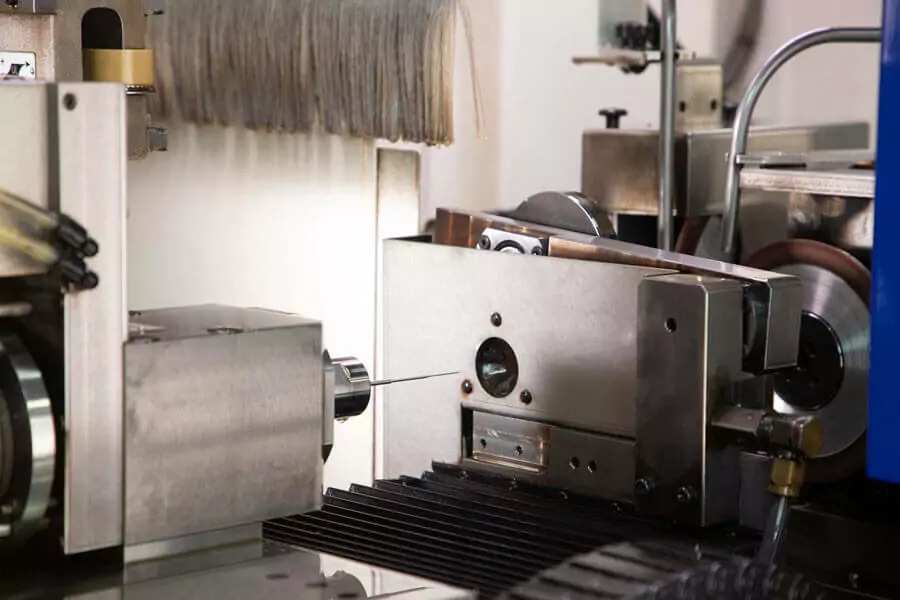
Our portfolio of CNC grinding machines includes the Swiss Rollomatic Shapesmart® NP5. This is a 5-axis cylindrical pinch/peel grinding machine with an integrated 3-axis robot loader, and is dedicated to cylindrical grinding of carbide, HSS and stainless steel components. Designed with a focus on the highest achievable surface finish and concentricity, the NP5 can perform a range of grinding tasks with diameters from 0.025 – 25 mm (.001″– 1″).
Technical Specifications For CNC Grinding Services
- ID / OD Grinding Tolerances ± 0.00007″ (±0.002mm)
- Roughness: Ra 0.08mm
- Cylindricity to ±0.0002″ (±0.005mm)
- Roundness to ±0.0002″ (±0.005mm)
- Materials Hardness: Up To HRA 94.5
Pinch & Peel Grinding For Rapid Cycle CNC Grinding
The “pinch and peel” method carries out rough grinding and finishing in one pass through the machine. This innovative method reduces cycle time by performing both processes simultaneously. On the NP5, two spindles are used to run a pair of different grinding wheels positioned on independently-controlled CNC linear slides. The first for rough grinding, and the second for the finishing pass.
Versatile Grinding Of Non-Round & Exceptionally Long Components
The Rollmatic NP5 can perform non round pinch/peel grinding of high precision punches and pins as well as non-standard shapes for molds, tool blanks and coolant slots. Pinch and peel achieves higher concentricity standards for long and thin parts than are possible with multi-pass grinding. Combined with the multi axis capabilities of the NP5, this opens up a wide range of CNC grinding applications across multiple industries:
- Exceptionally long & thin parts – total grinding lengths of 16” & blank length of 19”
- Form grinding of cutting tool blanks for industrial, medical & dental applications
- Production grinding of precision punches, including non-round, oblong & form punches
- Production grinding of die & mold components
- Can grind coolant slots in blanks with coolant through-holes
- Grinding of squares out of center, radiused corners, hexes & non-concentric cam profiles
Quality Control For Prototyping & Manufacturing
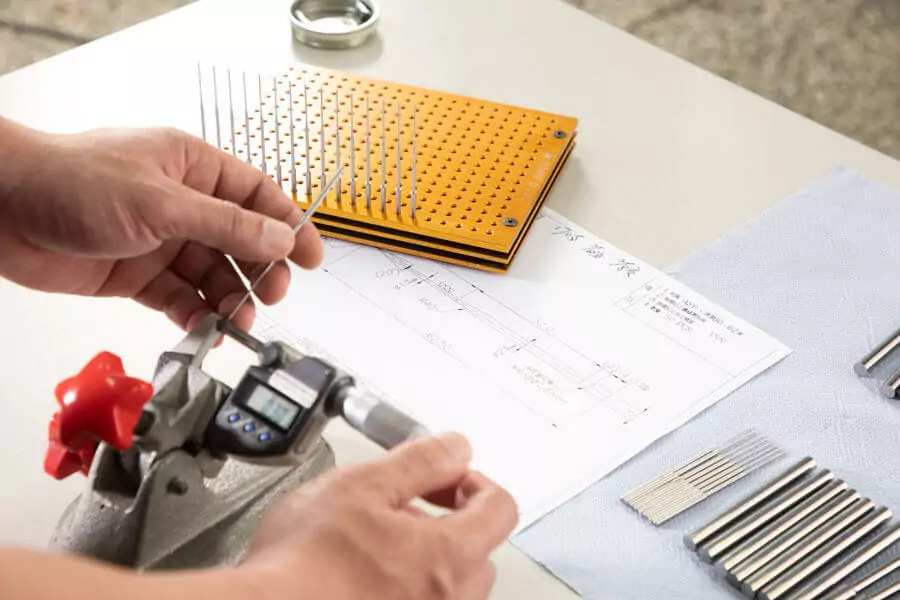
Quality control is an essential step in CNC machining and CNC grinding of intricate joints and critical surface finishes to precise geometric tolerances. We are equipped to carry out designing and prototyping of custom components as well as large scale production of precision finishes to the most recent ISO 9001:2015 standards.
Our 4 quality control measures for CNC grinding & CNC machining
- ISO 9001:2015 certified
- Auto & Manual QC
- 3D CMM Coordinate Measuring Machine
- Zero-Defect Shipments
Our quality control is exceptionally thorough, and we machine and grind parts to very precise tolerances with zero defects. Contact us now to discover how our precision CNC grinding services can meet and exceed your manufacturing requirements.