Hot runner systems are essential components of modern, high speed, efficient, injection molding. The quality of your hot runner system components determines the improvement to productivity and quality of manufacturing. JC Machining manufactures high precision hot runner components to exacting quality standards that ensure the smooth operation and clean, efficient, throughput you want for your injection molding processes.
Table of Contents
What is a hot runner system?
A hot runner system is made up of heated components that guide the molten plastic as it flows into the injection mold, and keep the plastic molten between injection molding cycles. This is different from traditional injection molding, which creates sprue and runners that cool and set with every production cycle and have to be removed in an additional production stage.
Hot runner system components are fed with molten plastic through a heated manifold. The molten plastic is directed into the cavities of the mold through channels. Hot runner channels have gates to control the flow, and shut off the flow when the cavity has been filled. The result is that the injection molded product is completed without remaining attached to a sprue.
The injection molding machine is programmed to open and close the hot runner gates and adjust the temperature of the hot runner system to ensure the plastic remains molten between cycles and exactly the right volume of plastic is injected at the correct pressure before the gates are closed. High precision hot runner components enable injection molding of complex and intricate products without leaving visible marks that show where the plastic was injected into the mold.
What are three advantages of hot runner injection molding?
- Shorter cycle times increase productivity
- No waste from sprues and runners
- Clean products with minimal finishing
Hot runner systems enable faster throughput, reduce plastic waste and regrinding, and can produce a very clean result that does not require additional finishing work. This makes them ideal for high volume production, especially of complex parts, and for production of delicate and intricate designs that are difficult to detach from a cold sprue without damage or distortion.
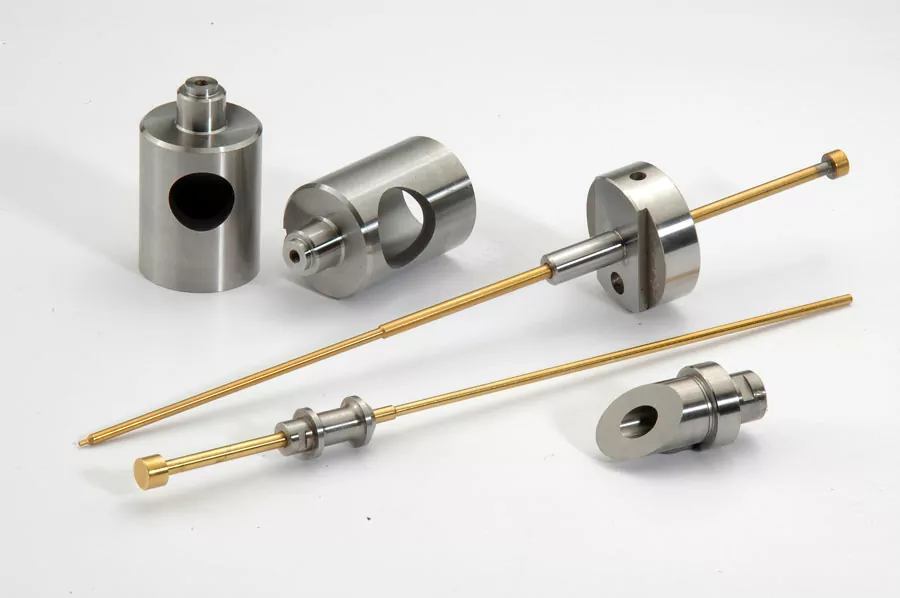
JC Machining Hot Runner System Component Manufacturing
We are experts in the manufacture of high quality hot runner system components, customized to meet any specific application. Our efficient CNC machining services are all in-house, ensuring rapid fulfillment of your order for hot runner system components, all backed by our zero defect guarantee.
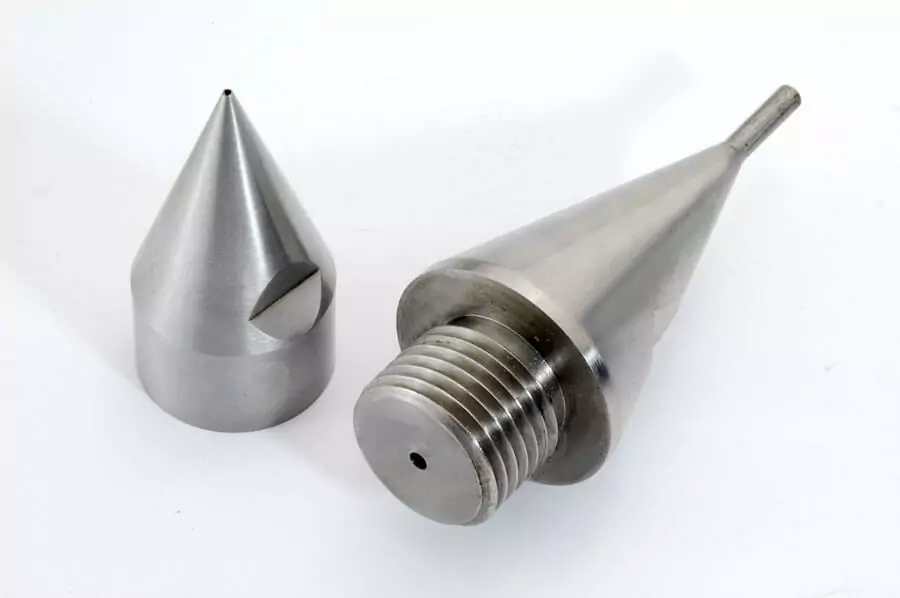
- nozzle tips
- nozzle tip insulators
- valve pins
- ejector pins
- nozzle housings
- valve bushings
- heating elements
- Thermocouples
- Retainers
- seal nuts
The hot runner nozzle tip shown here was manufactured by us in SDK61 using CNC turning and cylindrical grinding to a +/- 0.02mm tolerance. This example is shown as machined with no additional finishing or surface treatments.
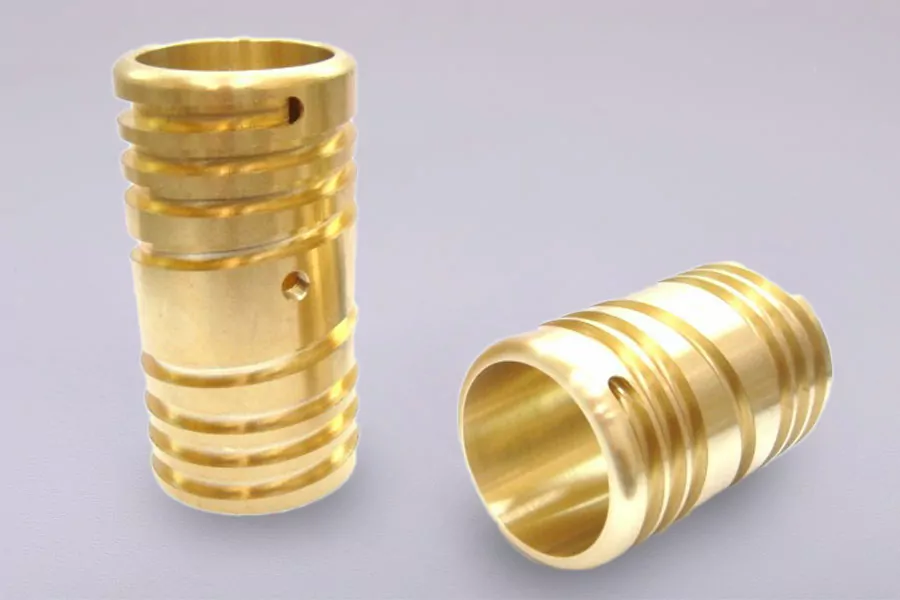
This copper heating element shows the excellent results possible in non-ferrous metals, with additional sandblasting after CNC turning, CNC grinding and surface grinding to achieve a +/- 0.01mm tolerance for our client.
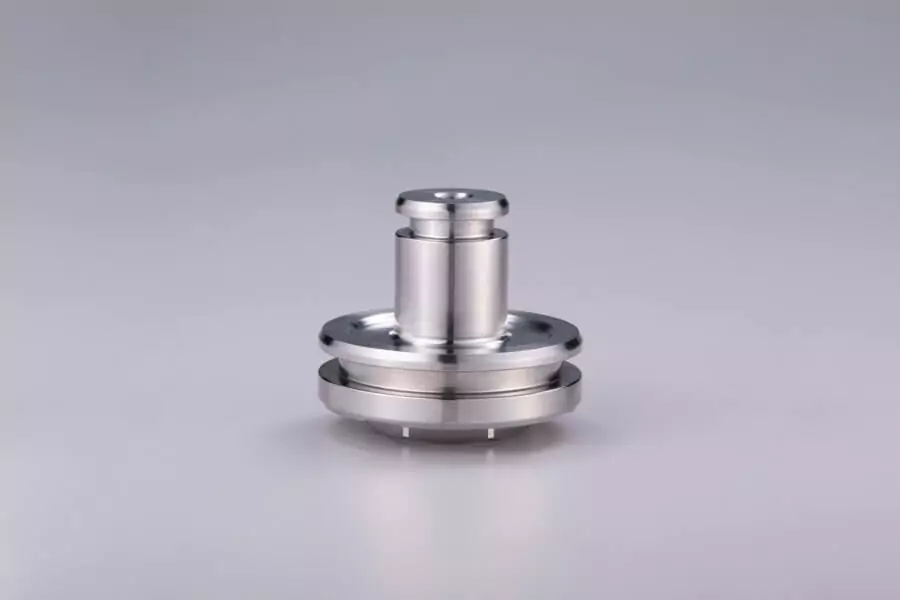
There is no compromise in manufacturing hot runner system pistons, which must be machined to very exact tolerances and finishes. This example has been CNC turned from SUS40 stainless steel to a +/- 0.01mm tolerance, and finished using cylindrical and surface grinding to achieve ARa 0.5-0.8 to ensure long life and reliable operation.
Experienced & efficient hot runner system component manufacturing
We maintain a comprehensive, modern suite of advanced CNC machines, and carry out all CNC machining processes in-house with no outsourcing. When you work with JC Machining you can expect the increased efficiency and quality control that comes from a team of experienced technicians who are dedicated to all stages of your project.
- Die Sink & Wire EDM Machining
- Optical Profile Grinding
- Tungsten Carbide Grinding
- CNC Turning
- CNC Milling
- CNC Grinding
Hot runner systems must be easy for mold makers to repair and maintain, with swift identification of necessary replacement parts. We manufacture all types of hot runner components as well as replacement spare parts for all hot runner systems to keep your production running smoothly.
Contact our expert technicians to discuss how we can satisfy your requirements. You can also upload a 2D or 3D design (CAD) file online, send us your drawings or samples to duplicate. We make it as easy as possible for you to get the results you want, and our zero defects guarantee ensures your complete satisfaction.