Surface grinding and centerless grinding services for industries including tool, die, and injection mold manufacturing
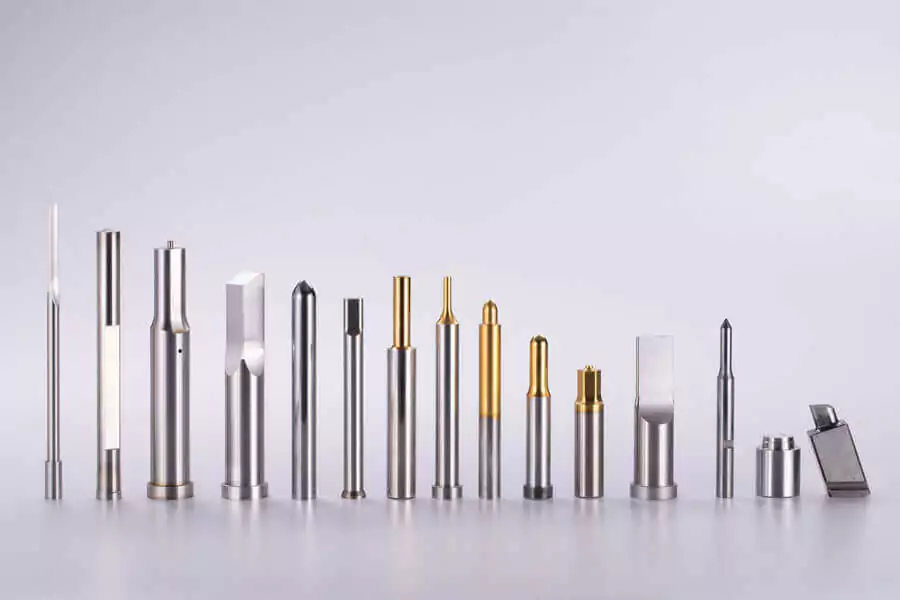
Surface Grinding & Centerless Grinding Services
Surface grinding and centerless grinding are two of the CNC machining and grinding services we offer to our global clients. Our grinding services include Optical Profile Grinding, Tungsten Carbide Grinding and CNC grinding. This complements our CNC Turning, CNC Milling, and EDM machining services to enable us to manufacture almost any product for our customers.
Table of Contents
What is surface grinding?
Surface grinding is a machining process that uses a rotating abrasive wheel to remove material from the surface of a workpiece to produce a smooth, flat finish. It is a versatile process that can be used to grind a variety of materials, including metals, plastics, and ceramics.
How does centerless grinding work?
In centerless grinding the workpiece rests on a blade without chucks or centers. Two wheels are positioned against the workpiece. One grinds the surface of the workpiece and the other controls the rotational movement of the workpiece. This makes it ideal for products that cannot be held between centers and also reduces setup time.
Achieving precision finishes by surface grinding
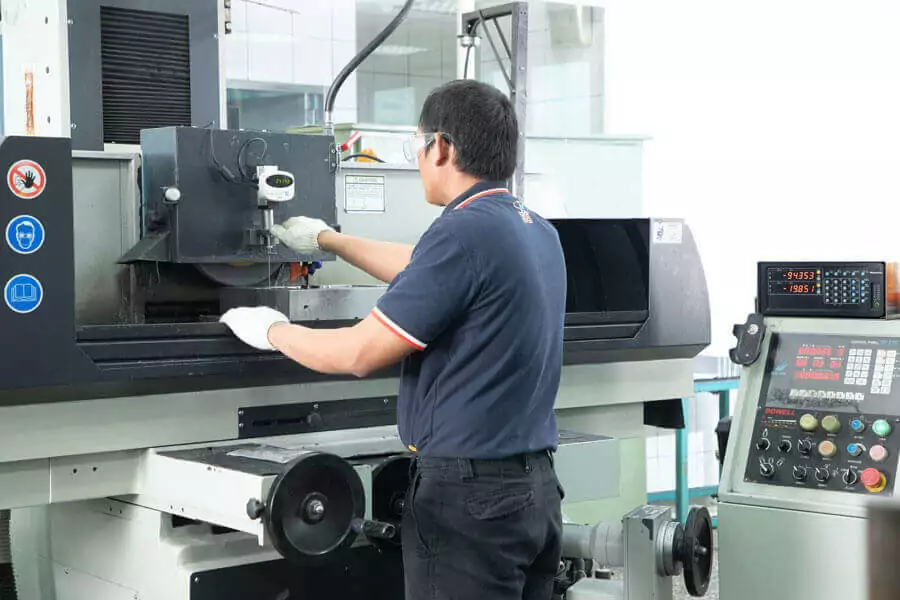
Surface grinding is a precision machining process that removes material by abrasion from the surface of a workpiece to achieve a flat, smooth finish. Metal, ceramic, and composite surfaces can all be ground with a high level of precision. Most surface grinding is carried out horizontally, with material removed by a grinding wheel rotating above and parallel to the work surface.
A very powerful magnetic plate is normally used to secure the workpiece in position under the grinding wheel, but mechanical vises and fixing methods can also be used. These are essential when cutting non-magnetic materials. Control systems for the movement of the workpiece and lowering of the grinding wheel are usually hydraulic, and semi or fully automated.
The rotating horizontal abrasive grinding wheel removes material from the workpiece as the workpiece is shuttled in a reciprocating movement under the grinding wheel. The type of material being ground and the desired surface finish dictate the specific type and size of the abrasive wheel needed to achieve the best results.
As the rotating grinding wheel is lowered onto the workpiece, it cuts into the surface, and the abrasive particles act like multiple cutting tools, shearing off chips from the workpiece. Depth of cut on each pass is controlled by manual or hydraulic adjustment of the vertical feed of the grinding wheel.
Coolant is used to lubricate the grinding process and keep both the abrasive wheel and the workpiece cool. This reduces the risk of distortion and heat damage to the workpiece, facilitates chip removal, and also helps to keep the surface grinding wheel clean and cutting at optimal performance.
Significant factors affecting the quality of finish when surface grinding
- grit size of the grinding wheel
- grinding wheel hardness
- speed of wheel rotation
- workpiece feed rate
- depth of cut at each pass
- coolant type and flow rate
Smoother finishes result from finer grit abrasives, with coarser grit used for more rapid removal of material for the workpiece. Relative hardness of the grinding wheel is an important consideration to control wheel wear. For this reason grinding wheels are manufactured with a wide range of abrasive coatings. Surface grinders may have horizontal wheel spindles, parallel to the work table, or vertical spindles, perpendicular to the work table. The configuration depends on workpiece shape and orientation.
Surface grinding enables the precision engineering of accurate, uniform and highly repeatable flat surfaces for the automotive, tool, die and injection mold making industries. Precision component finishes, and parts requiring exact dimensional tolerances are achievable with surface grinding because the process features very tight control over surface finish.
Centerless Grinding For Cylindrical Components
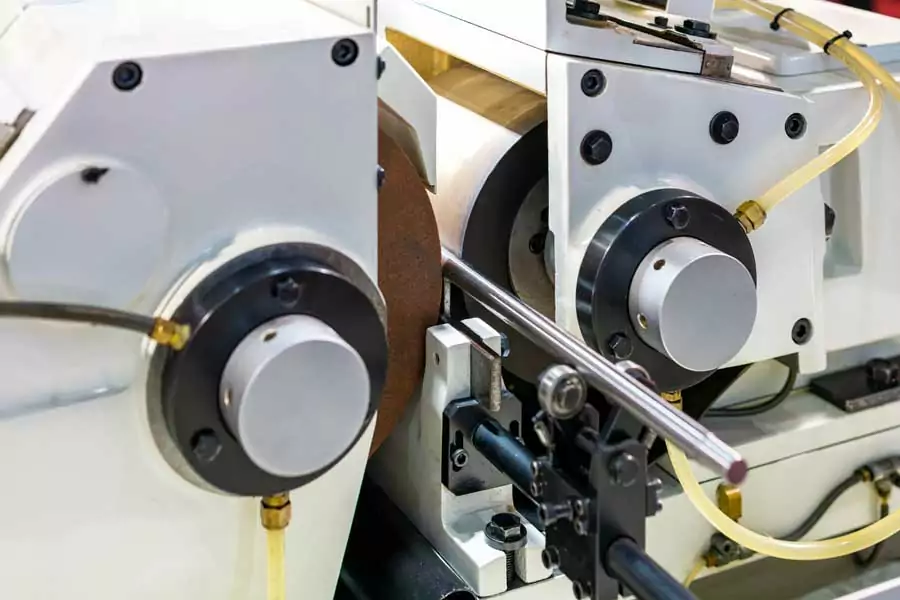
What is Centerless Grinding?
Centerless grinding is a machining process that uses abrasive cutting to remove material from a workpiece. The workpiece is held between two grinding wheels, which rotate in the same direction at different speeds. This creates a shearing action that removes material from the workpiece
As there is no requirement for time-consuming clamping of components, centerless grinding is useful for high volume production of cylindrical products that need to be processed rapidly and efficiently.
The workpiece is placed on a support (sometimes called a ‘knife’) between a movable regulating wheel and a grinding wheel which rotates around a fixed axis. The regulating wheel rotates at a slower speed than the grinding wheel and is movable to hold the workpiece against the grinding wheel. The distance between the two wheels is set by moving the regulating wheel to a specific measurement for the work in progress. This is called the grinding gap or work gap.
The regulating wheel rotates the workpiece to ensure even grinding and applies pressure to keep the workpiece in contact with the grinding wheel. Adjusting the pressure exerted by the regulating wheel on the workpiece controls vibration and modifies the rate of material removal during grinding, which determines the quality of finish.
The rotation of the grinding wheel removes material from the outer surface of the workpiece. The grinding wheel is manufactured from bonded abrasive compounds, with a hardness and composition matched to the specific material being ground to achieve the intended result. Correct setup of centerless grinding with appropriate wheel composition, rotation speed and regulating pressure, delivers excellent roundness to tight tolerances.
The blade or work rest supports the workpiece and guides it through the grinding gap. This provides stability and helps align the workpiece during the grinding process. With through grinding, it also increases control of the feed rate of the workpiece and prevents flexing and misalignment.
The main advantage of centerless grinding is that it removes the requirement for a chuck or center clamping device to hold the workpiece in position. As well as increasing productivity, this enables continuous ‘through feed’ grinding of long workpieces.
Centerless grinding offers many advantages compared to traditional grinding
- high-volume & mass production capability
- reduced setup times
- automated or semi-automated processing for continuous operation in production lines
- excellent concentricity and dimensional accuracy
- through-feed grinding of long workpieces
Centerless grinding is excellent for applications that require precise cylindrical components. It is particularly suitable for grinding:
- tools, punches, rods, bushings & pins
- engine pistons, shafts, valves & rods
- roller bearing parts
- cylindrical shafts, bars and tubes
- long & slender parts
Centerless grinding is a highly reliable, consistent, and efficient process for machining to tight tolerances with excellent surface finishes. This makes it an excellent option for all modern manufacturing including automotive, medical, tool and die industries
Grinding Services From JC Machining
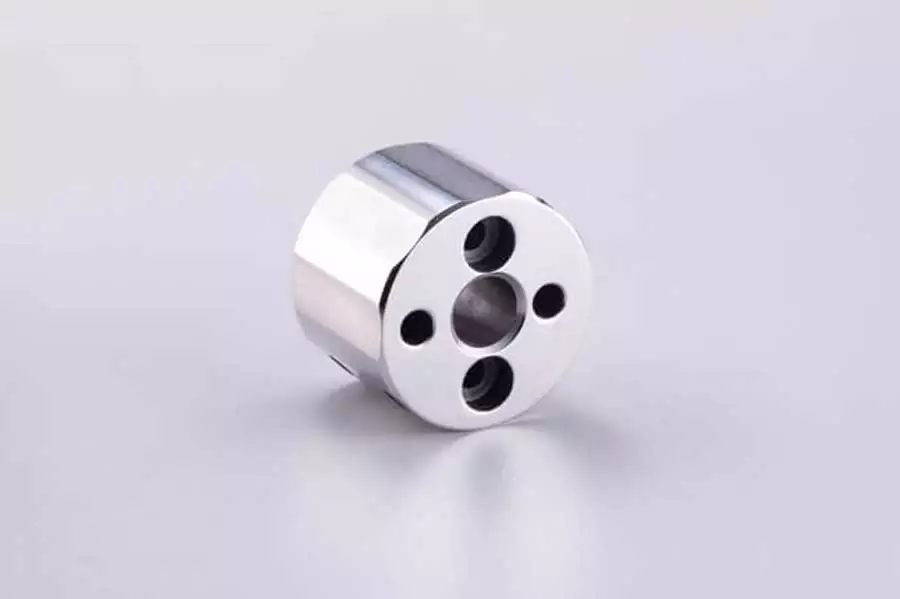
Our grinding services can be used to manufacture parts in metals, plastics, and ceramics for many different industries. Our experience includes manufacturing engine parts, injection molding components, medical tools and implants, and semiconductor and electronic components.
Typical applications of CNC grinding and machining services
- high precision injection mold parts
- precision machine components
- tools, punches and dies
- medical instruments, implants & devices
- semiconductor & electronic components
- automotive engineering parts
High Precision Grinding Technology
Our CNC grinding machines can perform highly specialized, small cylindrical grinding operations, including complex shapes and forms. Our precision grinding experience enables us to achieve very fine surface finish requirements, with standard tolerances in excess of most industry requirements.
Technical Specifications For Surface & Centerless Grinding Services
- Materials Hardness: Up To HRA 94.5
- ID / OD Grinding Tolerances ± 0.00007″ (±0.002mm)
- Roughness: Ra 0.08mm
- Roundness to ±0.0002″ (±0.005mm)
- Cylindricity to ±0.0002″ (±0.005mm)
Technical Specifications For Surface & Centerless Grinding Services
- Materials Hardness: Up To HRA 94.5
- ID / OD Grinding Tolerances ± 0.00007″ (±0.002mm)
- Roughness: Ra 0.08mm
- Roundness to ±0.0002″ (±0.005mm)
- Cylindricity to ±0.0002″ (±0.005mm)