Stamping and pressing are among the most important and widely used techniques for forming and molding sheet metals, especially for low cost, high volume manufacturing. The dimensional accuracy of press stamping mold components is critically important, as very small variations and errors in manufacturing will result in sub-standard products and excessive mold wear, requiring frequent and potentially costly re-tooling.
Table of Contents
Precision manufacture of press stamping mold components
We produce press stamping mold components with 2µm tolerances at our state of the art CNC machining service in Taiwan. All stages of component machining are carried out in-house to exacting quality standards. We can do this because we maintain a comprehensive inventory of CNC machining equipment, which keeps your project under total quality control with us from the first to last step in the process from reviewing the design through to shipping of the finished product.
What is press stamping?
In press stamping, sheet metal is placed on a mold in a stamping press. The mold composes tools and dies that are machined to form the sheet metal into the desired shape by a combination of techniques including punching, bending, blanking, drawing, embossing, flanging and coining. In the forming process, the metal sheet changes thickness and distorts as it is compressed against these tools and dies by the press.
Progressive stamping and four-slide molding enable the manufacturing of hard-to-form and complex products with the high speed and accuracy advantages that are inherent in press stamping and sheet metal molding using high quality, precise, molds and components.
Understanding and allowing for the way in which different metals change as they are formed into new shapes is an important element of press stamping mold component design, and is why press stamping mold components need to be manufactured to very high standards of precision. This is especially important in contemporary manufacturing processes, which aim to minimize material use and material waste, approaching the forming limit without compromising the performance or strength of the finished product.
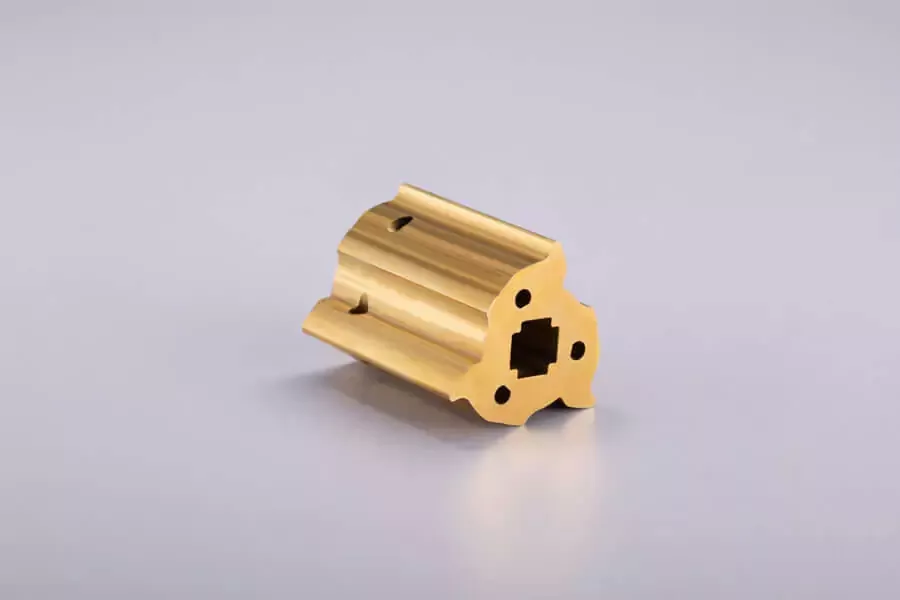
Optimized press stamping mold component manufacturing
Every project we undertake is carefully reviewed by our expert team, drawing by drawing, to find potential design enhancements and identify the best machining processes to produce the components you want, with the quality you need at the best possible price. Our professional engineers and machinists work with you to reduce manufacturing redundancy, optimize CNC programming, shorten machining time, improve surface finish, and deliver the best quality machined parts.
During the manufacturing process, your project is barcode registered, tracked, and continuously verified against our zero defect quality control guarantee. You can call or email us at any time, and we can immediately update you on your projects in progress, offer design feedback and material recommendations for new projects, and answer any questions you may have about our services and capabilities.
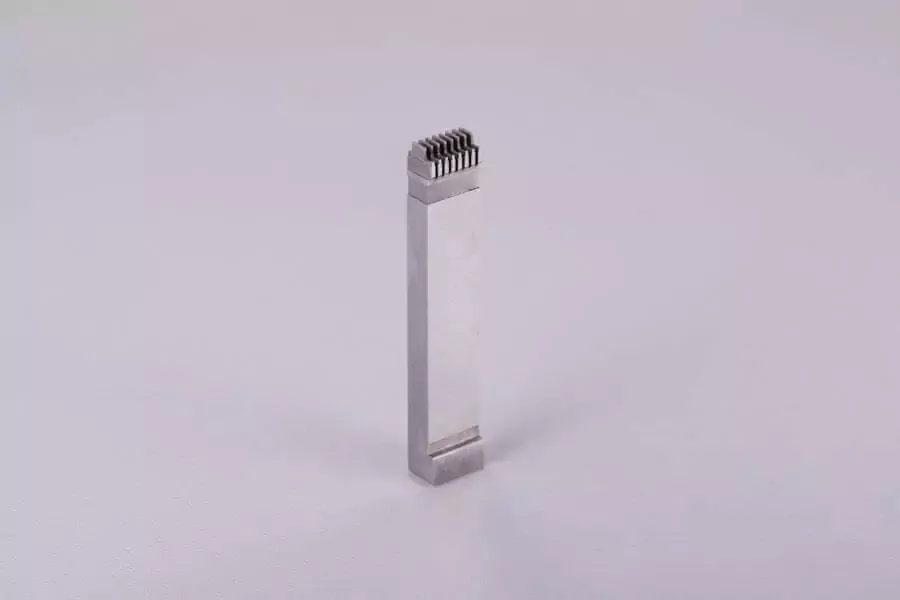
What processes are used to manufacture press stamping mold components?
The diversity and complexity of press stamping molds in 2024 requires the use of every type of CNC machining and grinding technology to get the best and most accurate results. CNC milling and turning are often used for shaping the bulk of a stamping mold, but for high precision components and intricate parts EDM machining is an essential tool in the manufacturing process.
- Die Sink & Wire EDM Machining
- Optical Profile Grinding
- Tungsten Carbide Grinding
- CNC Turning
- CNC Milling
- CNC Grinding
To achieve mirror-like surface finishes or complex textures, optical profile grinding and tungsten carbide grinding are often used. The surface finish of stamped and molded metal sheet products depends on the quality of the mold and press stamping component surfaces. A high precision press stamping mold eliminates the need for additional surface finishing.
To experience the benefits of working with JC Machining to meet your press stamping mold component needs, you can contact one of our technicians, or simply upload a 2D or 3D design to our secure portal for discussion and feedback. We are more than happy to apply our extensive knowledge and practical experience to optimizing your designs, and with our integrated in-house service you can expect personalized and well-informed communication and updates at every stage of your project.